MAN Truck & Bus lanserade officiellt sin batteritillverkning på produktionsanläggningen i Nürnberg den 11 april. Under evenemanget tillkännagav den München-baserade kommersiella fordonstillverkaren MAN nästa expansionssteg av sin batteriproduktion i Nürnberg för första gången.
Utöver de cirka 100 miljoner euro som redan har investerats i produktionsanläggningen som nu har lanserats, kommer ytterligare 150 miljoner euro att investeras under de kommande åren för att vidareutveckla expertis inom batteriteknikområdet och öka mervärdet. Detta görs samtidigt som man investerade i dieselmotortillverkning.
Konkret innebär det bland annat att förutom batteripaketen som består av flera moduler kommer att produceras i Nürnberg för nästa batterigeneration.
Av de aviserade tilläggsinvesteringarna på totalt cirka 150 miljoner euro kommer cirka 18 miljoner euro att subventioneras. Både det federala ministeriet för ekonomi och klimatskydd (BMWK) och delstaten Bayern tillhandahåller finansiering. Dessutom finansierar Bayern vidareutveckling av och forskning om batteriteknik på MAN-anläggningen i Nürnberg med cirka 30 miljoner euro.
Dessa medel kommer att användas till forskning inom områden som batterimontering, cellkemi och åldrande samt batterisäkerhet. Sammantaget kommer investeringarna i Nürnberg att säkra cirka 400 jobb i en framtidsteknik och ytterligare främja omvandlingen av platsen. De anställda som arbetade inom batteriproduktion var tidigare sysselsatta inom områdena motormontering, gjuteri eller logistik och kunde tack vare omskolning öppna upp ett nytt framtidssäkert arbetsfält för sig själva.
Starten av batteriproduktionen är den andra nya produktionslinjen som öppnas i Nürnberg i år. Tillverkningen av den senaste generationen MAN-dieselmotorer som används i den nya D30 PowerLion-drivlinan är också en investering för framtiden och säkrar många jobb på platsen.
MAN har investerat cirka 250 miljoner euro i detta projekt.
MAN antar för närvarande att nästan hälften av lastbilarna i Europa och cirka 90 procent av stadsbussarna kommer att levereras med nollutsläppsdrivsystem till 2030. Den högeffektiva, bränslesnåla D30-motorn kommer därför fortfarande att behövas långt in på 2030-talet. Även andra motorplattformar och serier kommer på sikt att finnas tillgängliga i MAN:s externa motorverksamhet.
På MAN-anläggningen i Nürnberg tillverkas batteripaket i tre så kallade formfaktorer. En platt formfaktor används i MAN Lion’s City E, den batterielektriska stadsbussen. Två andra formfaktorer används i MAN eTGL, MAN eTGS och MAN eTGX eTrucks med totalvikter på 12 till 50 ton. Starten av serieproduktion av MAN eTrucks eTGS och eTGX i München är planerad till juni i år.
I det nuvarande utbyggnadsskedet kan 50 000 batteripaket produceras per år i Nürnberg. Den nya M50-byggnaden är dock designad för att kunna producera 100 000 enheter per år. Batteriproduktionen kommer att skalas upp beroende på efterfrågan på batteridrivna fordon.
MAN använder NMC-cellkemi (’nickel-mangan-kobolt’) i sina batterier vilka är särskilt anpassade för drift av kommersiella fordon. Batterihanteringssystemet (BMS) övervakar kontinuerligt cellernas tillstånd under drift. Om exempelvis en oförutsedd händelse inträffar vidtar den interna åtgärder för att säkerställa ett säkert laddningstillstånd.
I händelse av en olycka kopplar BMS omedelbart bort batteriet från resten av fordonet (högspänningsnödavstängning). Den använder också ett intelligent värme- och kylsystem för att hålla battericellerna i ett optimalt temperaturområde hela tiden.
Modultillverkning är en teknisk höjdpunkt i den storskaliga produktionen av batteripaket som nu startar. Det innebär att MAN arbetar med ett system som klarar olika produktvarianter och enkelt kan anpassas till nya varianter oberoende av varandra.
Kvalitet och säkerhet har högsta prioritet och det gäller även ny batteriproduktion. Varje batteripaket genomgår ett ”end of line”-test i slutet av produktionen. Fokus ligger här på olika mjukvarutester, elektriska tester som laddning/urladdning, kontroll av data för battericeller och moduler som överförs av leverantören och ett läckagetest.
Varje batteri utsätts för ett testprogram om 23 punkter och cirka 400 testparametrar registereras. Detta dokumenteras individuellt för varje batteri och gör det möjligt att spåra produktionsprocessen även efter 15 år.
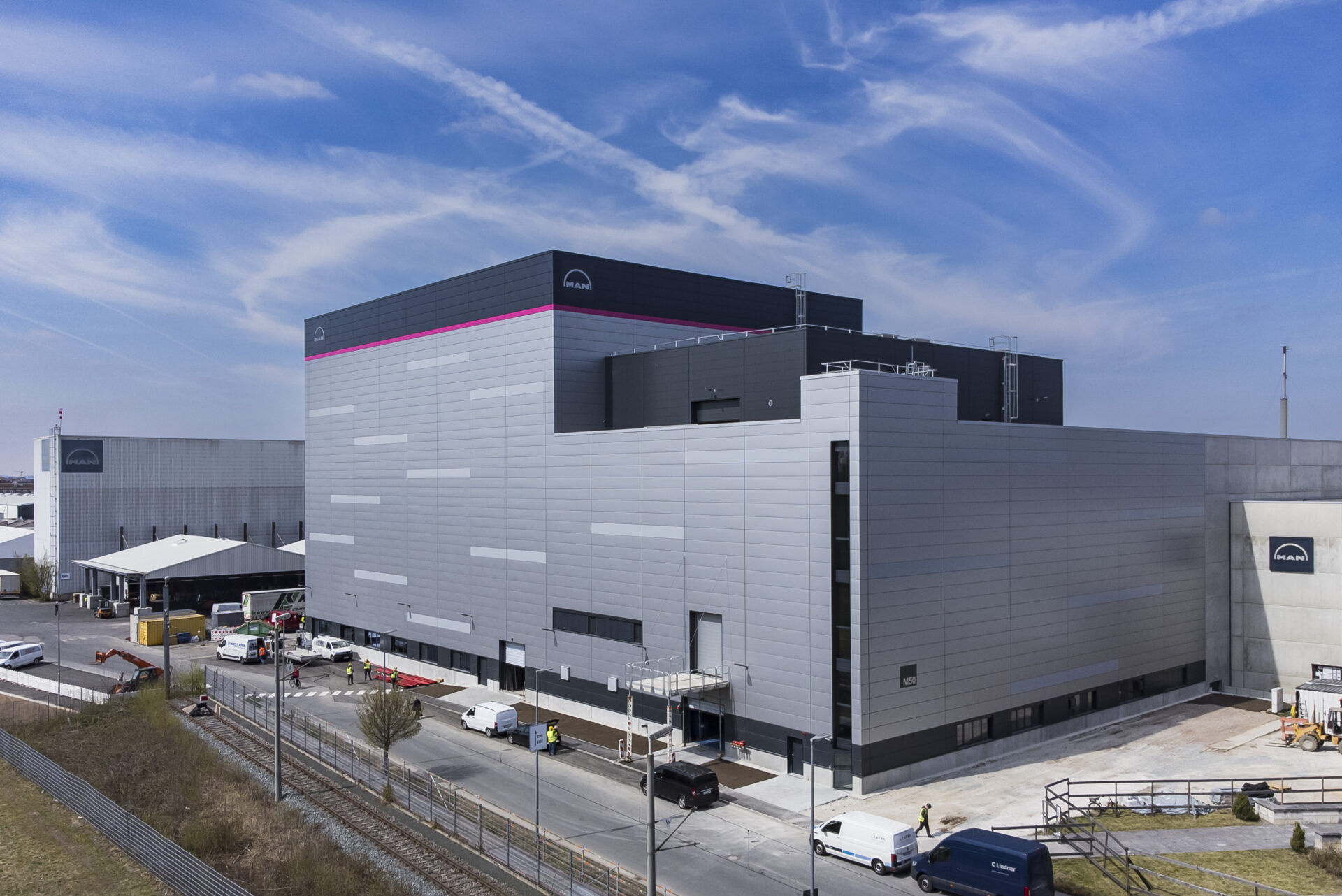
Anläggning i Nürnberg beräknas ge cirka 400 jobb. Foto: MAN Trucks.